Manitowoc’s Product Verification Centers have helped the company design and manufacture the most reliable cranes to ever be produced.
A crane can only be as good as the sum of its parts. For almost eight years, Manitowoc has been putting this idea into practice at its Product Verification Centers around the world. These multimillion-dollar, state-of-the-art testing facilities rigorously scrutinize the components that go into its cranes, ensuring that they meet the highest standards of quality and reliability.
Manitowoc has five Product Verification Centers in locations around the world, including: Shady Grove, Pennsylvania, U.S., Wilhelmshaven, Germany; Charlieu, France; Lusigny, France; and Zhangjiagang, China. All are housed in their own buildings, near Manitowoc’s manufacturing facilities in these cities. As various models of cranes are produced at different locations, a Product Verification Center near each factory ensures that components are being fully tested for all of Manitowoc’s crane lines.
This rigorous testing of component performance and working life cycles gives Manitowoc engineers insight into the anticipated performance of Manitowoc, Grove, National Crane and Potain cranes in the field. This process performance also speeds up product development for new designs, reduces warranty claims and on-site stoppages, and enables the direct comparison of supplier components.
The Product Verification Centers test component designs earlier in the product development process than previously possible. That means component suppliers can be vetted before the products are placed in cranes. The head start enables Manitowoc to discover any potential difficulties at an earlier stage and work closely with component suppliers to devise solutions long before equipment reaches job sites.
Barry Pennypacker, president and CEO of The Manitowoc Company, said that the testing processes at the Product Verification Centers have helped the company deliver on the promise of The Manitowoc Way.
“The Manitowoc Way operating system has increased the velocity of our product development, so we are able to bring new cranes to the market much faster,” he said. “The testing performed at the Product Verification Centers ensures that the cranes we are producing are reliable down to the component level, and this gives us the utmost confidence in introducing new cranes. We know that our cranes bring a level of quality to the job site not previously seen in the lifting industry.”
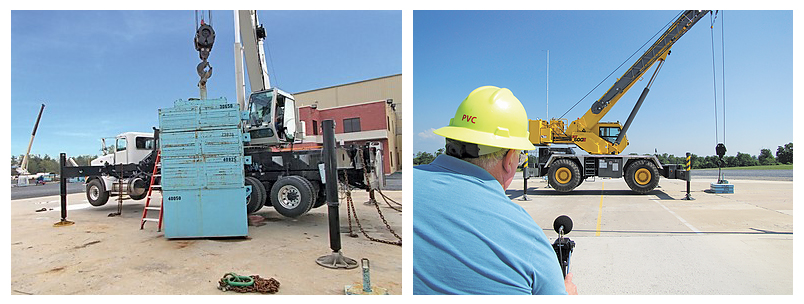
A look inside
At each Product Verification Center, there are specially trained staff, with dozens of managers, technicians and engineers contributing to the processes. A proprietary verification management system organizes, prioritizes, summarizes, compares and archives the centers’ test results. Manitowoc then shares its results with its suppliers, further strengthening its relationship with these companies, and also providing valuable insight that can help them improve their component production.
The Product Verification Centers feature a number of technologies that deliver detailed pictures of anticipated component performance. Among the most significant are:
• Severe environment test (HALT) chambers that can mimic extreme temperature swings and test component reaction to continuous vibration
• Walk-in temperature and humidity chambers that are large enough to fit entire crane cabs, consoles and power boxes
• Structural test systems with state-of-the-art data acquisition systems
• Electrical and software testing labs
• Imaging systems for forensic analysis, including a thermal imaging camera and microscopes
• Materials lab with chemistry analysis and material strength equipment, flaw detector and hardness tester
• Cyclic corrosion chambers that recreate saltwater exposure and corrosive conditions
• Modular test benches for fatigue testing that improves engineering calculation models and accelerates time dedicated to new developments
• Gantries that perform 24/24hr endurance tests on hoist mechanisms
These facilities enable the testing of entire cranes, too. Engineers can view cranes being tested on one of the center’s test pads, for example, and monitor the results in real time. The test centers allow for the full extension of crane booms, so engineers can accurately re-create jobsite conditions.
A look back
Manitowoc has had a long history with component testing, beginning decades ago at its facilities in France and the U.S. The company discovered that many of its suppliers couldn’t test their own products and when they did, the measurements were often incomplete. Driven by the desire to understand as much as possible about each component that goes into a Manitowoc crane, the company decided it should create its own verification facility. It started planning for the first standalone Product Verification Center in 2009 as part of its commitment to continuous quality improvement.
In 2012 Manitowoc opened its first official Product Verification Center at its Shady Grove factory in Pennsylvania. The facility was the first of its kind in the industry and provided unprecedented component testing capabilities. The first Product Verification Center saw great success, providing immediate insight into Manitowoc’s crane design and production processes. The program was so successful that Manitowoc decided to expand the operation.
Having monitored the success of our Product Verification Center in the United States, the company felt the time was right to expand the concept with additional facilities. With the continued focus on innovation and lean manufacturing, as well as bringing several industry-leading models to market, additional Product Verification Centers in multiple regions would expand the company’s capacity for component testing.
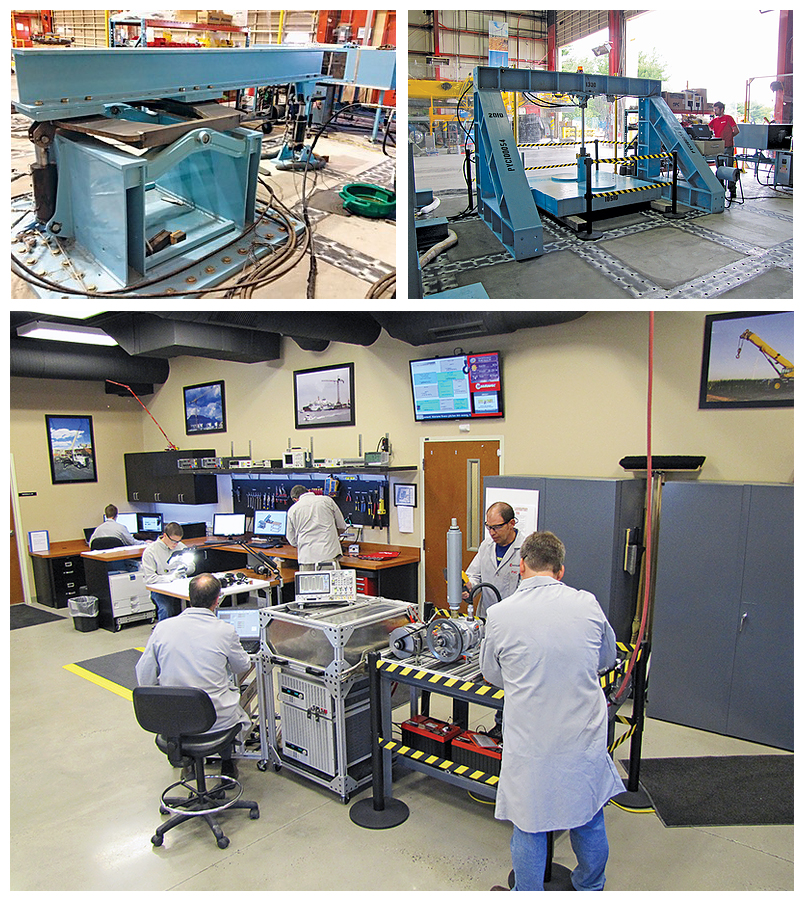
In the ensuing years, Manitowoc opened Product Verification Centers in Wilhelmshaven, Germany, and then began overhauling and improving its original testing facilities in Charlieu, Lusigny and Zhangjiagang to bring them in line with the new Product Verification centers in the U.S. and Germany.
Teams of highly qualified engineering personnel ensure that the Product Verification Centers in all these countries seek to test supplier components and crane functions to the highest levels of scrutiny. These teams include experts in assembly, erection, welding, mechanical engineering, hydraulics, electronics, vibro-acoustics and more.
“By rolling out our testing and verification processes to Product Verification Centers across the globe, we have been able to replicate our success in improving component quality while increasing the quality and durability of our products,” Pennypacker said. “It was the right move to strengthen our position in all of these countries, and it has helped us ensure our position as one of the world’s leading producers of cranes.”